Buen día amigos de Steemit, hoy les traigo una simulación que hice para poder hacer una comparación entre dos métodos termodinámicos muy utilizados en mezclas de hidrocarburos, debido a la serie de post que he colocado anteriormente haciendo un estudio de las torres desbutanizadoras en una planta de olefinas. Ahora bien, no solo fue importante saber cuáles son las variables que interfieren en el buen funcionamiento de la misma, sino también buscar cómo solucionarlos. A continuación explico cómo se hizo la simulación para concluir un buen método que pueda llevarnos a conseguir mejoras en el sistema. #stem-espanol #steemstem
Inicialmente, se realizó la simulación del proceso de una Columna Desbutanizadora empleando el software Aspen Plus V7.3, utilizando los modelos termodinámicos Peng-Robinson y Soave–Redlich–Kwong (utilizado para mezclas de hidrocarburos). La elaboración de la simulación de una torre desbutanizadora con dos métodos termodinámicos se realiza con el fin de comparar cual modelo es el más idóneo para determinar el buen funcionamiento de la columna y hacer las diferentes modificaciones que proporcionen el desarrollo de mejoras en todo el proceso.
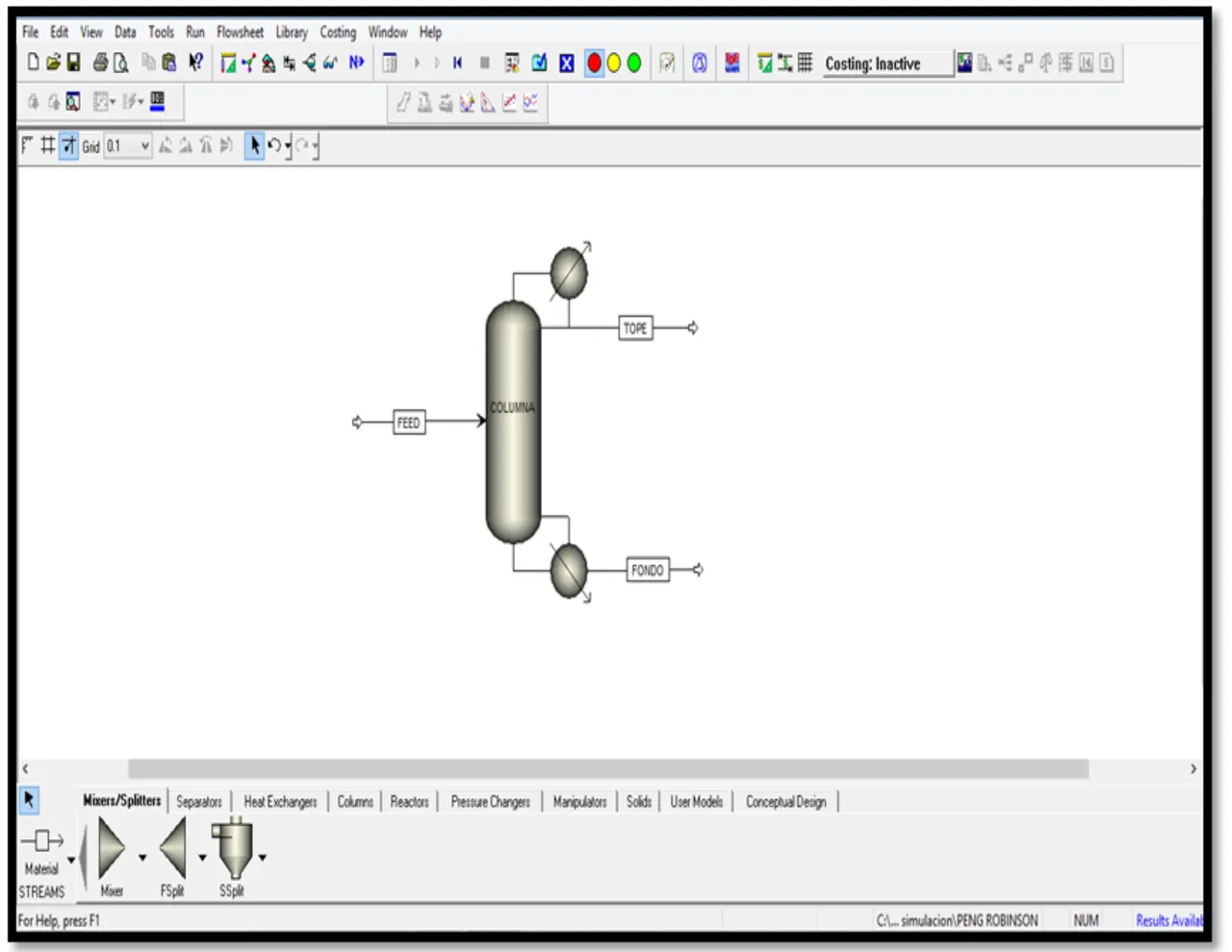
Figuera 1. Diagrama del proceso de separación característico de una torre desbutanizadora generada en el simulador Aspen Plus.
Fuente: @rossanavictora
En cuanto a los datos requeridos para la simulación de la torre desbutanizadora, estos se muestran en las siguientes tablas:
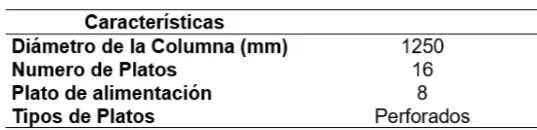
Tabla 1. Características de diseño típico de una torre desbutanizadora.
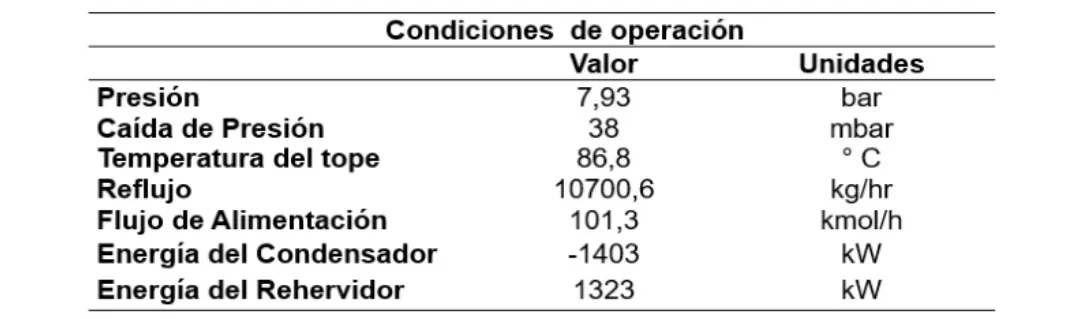
Tabla 2. Condiciones de operación típica en una columna desbutanizadora.
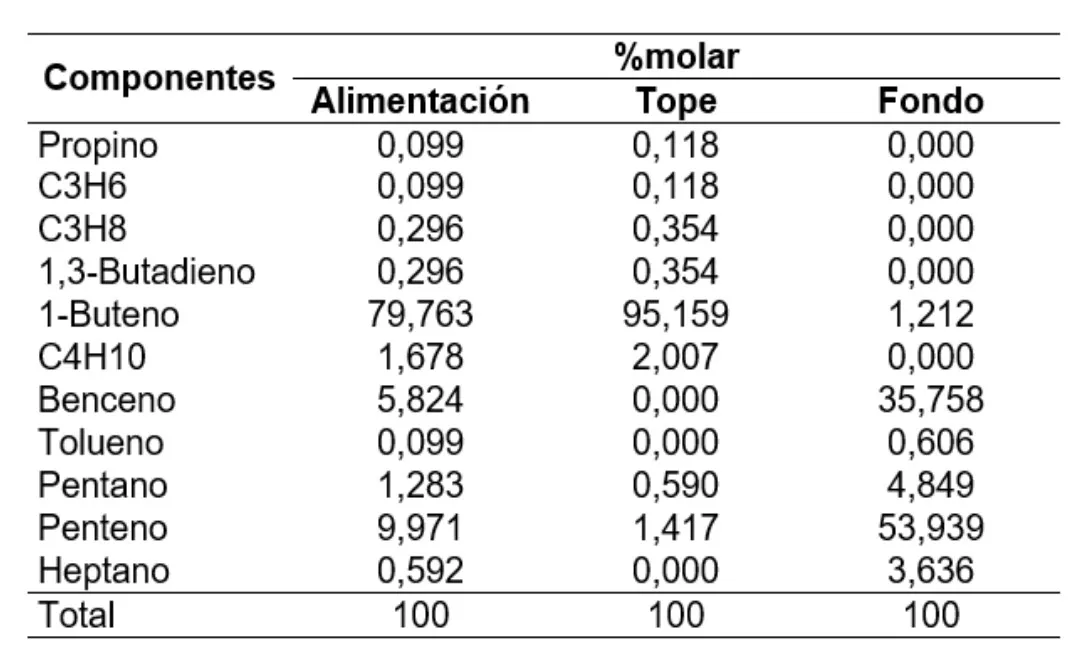
Tabla 3. Balance de masa típico en una columna desbutanizadora.
A continuación se presentan dos tablas en las que se exhiben las desviaciones que se derivan de los dos métodos termodinámicos utilizados para estas simulaciones (Peng Robinson y Soave- Redlich–Kwong). En la tabla 4, se visualiza el porcentaje de desviaciones existentes arrojadas por el simulador utilizando Peng Robinson, mientras que en la tabla 5, se muestran los resultados del porcentaje de desviaciones generadas por el método termodinámico Soave–Redlich–Kwong en comparación con el de diseño típico.
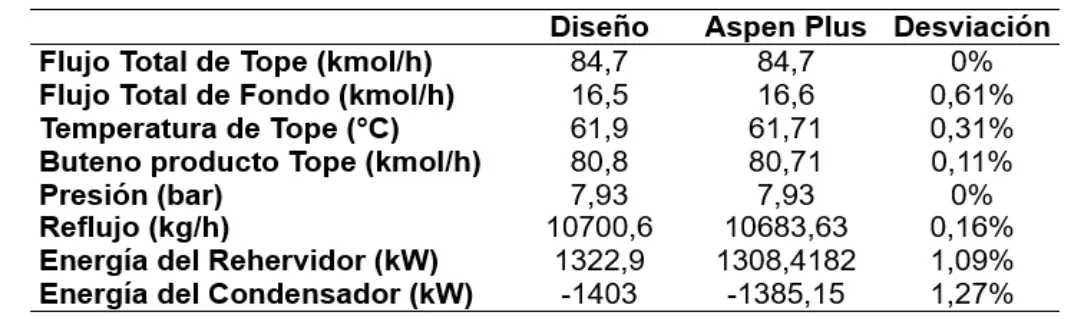
Tabla 4. Porcentaje de desviación entre Aspen Plus y condiciones de diseño. (Peng Robinson).
Fuente: @rossanavictora
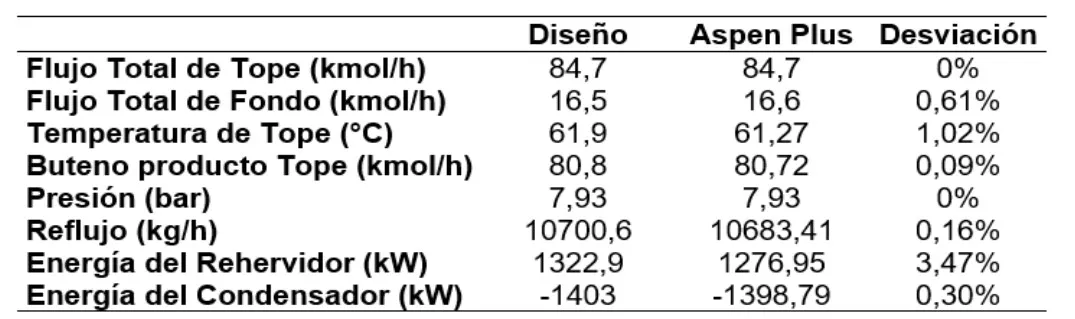
Tabla 5. Porcentaje de desviación entre Aspen Plus y condiciones de diseño. (Soave- Redlich–Kwong).
Fuente: @rossanavictora
Es importante acentuar, que estas simulaciones se ejecutan con la finalidad de obtener las composiciones y datos de fondo de diseño de la columna desbutanizadora. Por tal motivo fue necesario efectuar diversos balances de masa que generaran la alimentación acertada para validar el proceso, además de realizar cálculos para la obtención de la relación de reflujo a través del flujo molar del líquido que ingresa nuevamente a la torre como reflujo entre el destilado (producto tope – reflujo) generado por la columna, ya que no se contaba con dicha información. De esta manera, trabajar con valores exactos que no desalineen la simulación arrojando resultados erróneos que compliquen la investigación.
Luego de ser ejecutadas las simulaciones con ambos métodos termodinámicos se observa que los resultados arrojados entre ambos son aptos para la realización del estudio, puesto que ninguno excede el 5% de porcentaje de desviación lo cual hace válido el proceso con los datos proporcionados al simulador. Así mismo, se puede visualizar en las tablas 4 y 5 que hay diferentes porcentajes de desviación en las condiciones operacionales utilizadas para las simulaciones con los dos métodos termodinámicos, presentándose en la de Peng Robinson mayor desviación en la energía del condensador, mientras que en la de Soave – Redlich – kwong la mayor desviación se percibe en la energía proporcionada por el rehervidor. Sin embargo, para realizar el correcto estudio de esta investigación; el método más conveniente es el Peng Robinson, puesto que las condiciones de operación son las que presentaron menor desviación comparadas a las de diseño.
Por consiguiente, los valores tomados de los balances se presentan en flujo molar; pero fueron llevados a porcentaje molar para una mejor visualización de los cambios de composición resultados en el tope y fondo a través de la simulación tal y como se muestra en las tablas 3 y 6. Cabe destacar, que en la tabla 3 se puede observar el balance de masa en porcentaje molar a condiciones típicas de diseño, mientras que en la tabla 6 se distinguen los cambios que proporciona el simulador con los datos típicos de la torre desbutanizadora asignados al mismo.
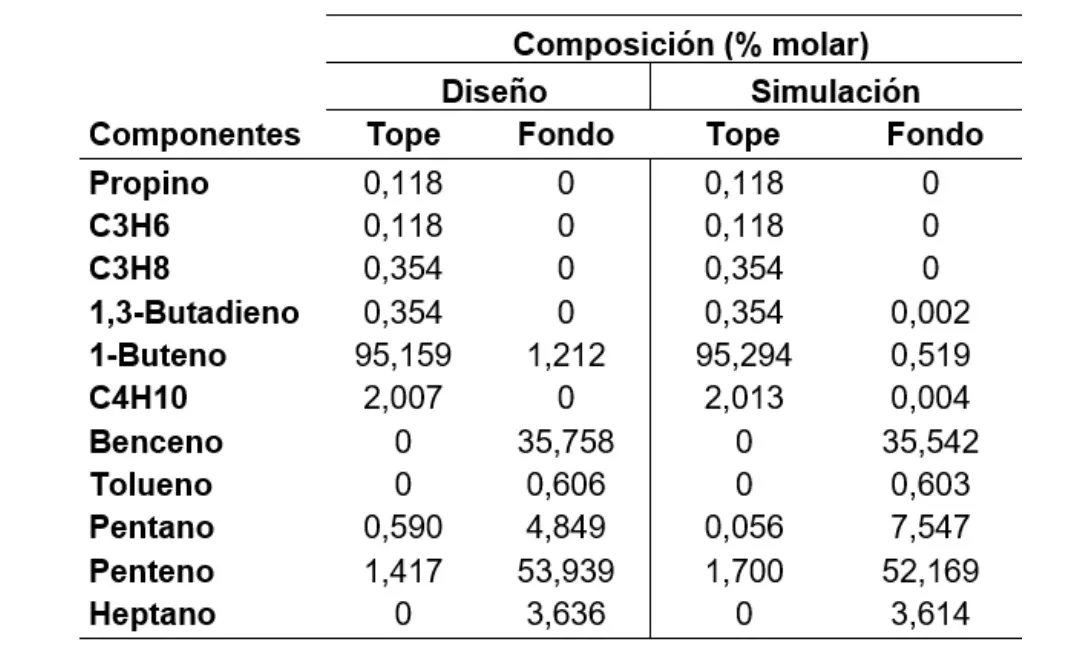
Tabla 6. Balance de masa arrojada por el simulador ASPEN PLUS.
Fuente: @rossanavictora
Como se observó en las tablas anteriores no hay mucha desviación entre lo que nos indican los datos característicos de diseño comparándose con las derivaciones arrojadas por el simulador. Del mismo modo, es importante tomar en cuenta el perfil de temperatura arrojado por el simulador en cada etapa de las columnas. En dicho perfil se puede monitorear e interpretar la temperatura de los fluidos a medida que se mueve entre la etapa de rectificación y agotamiento de las torres generalmente. Los datos numéricos recolectados se muestran a través de una gráfica en la figura 2, donde se puede apreciar los diferentes cambios de temperatura en cada plato del proceso. Con estos análisis se indica cual podría ser el perfil ideal para establecer las condiciones correctas a las que puede funcionar adecuadamente el proceso de separación de butanos.
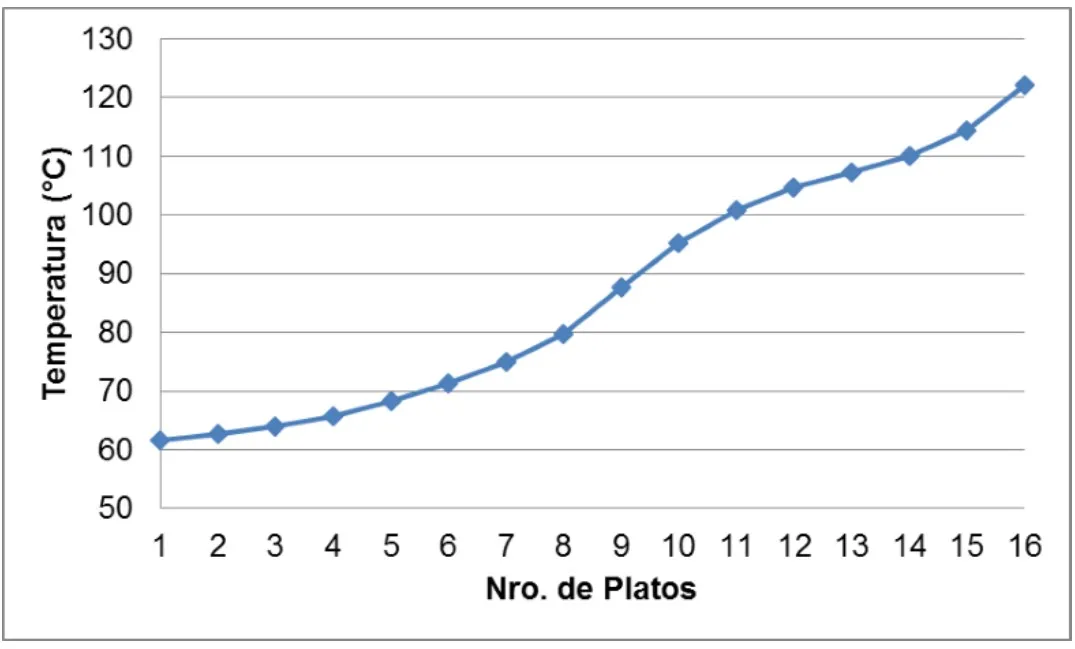
Figura 2. Perfil de temperatura típico en las torres desbutanizadora por simulación.
Fuente: @rossanavictora
Por otra parte, la estabilidad de la columna se ve representada en la variación de las fases de los fluidos, debido a que en cada plato se produce la separación de los mismos, haciendo uso de las diferentes volatilidades de los distintos componentes. Las columnas de destilación de butanos transfieren la cantidad necesaria de energía, consiguiendo llevar las composiciones que generalmente fluyen en mencionadas torres a un estado de vapor o líquido, donde los componentes más ligeros se quedan en la fase de vapor y los más pesados en la fase líquida. En las figuras 3 y 4, se puede apreciar la fluidez de estos cambios en cada plato del sistema de destilación de butanos, viéndose que los componentes más ligeros como el 1- buteno, van disminuyendo en las corrientes de líquido y vapor. Mientras que los componentes más pesados como el penteno, van aumentando.
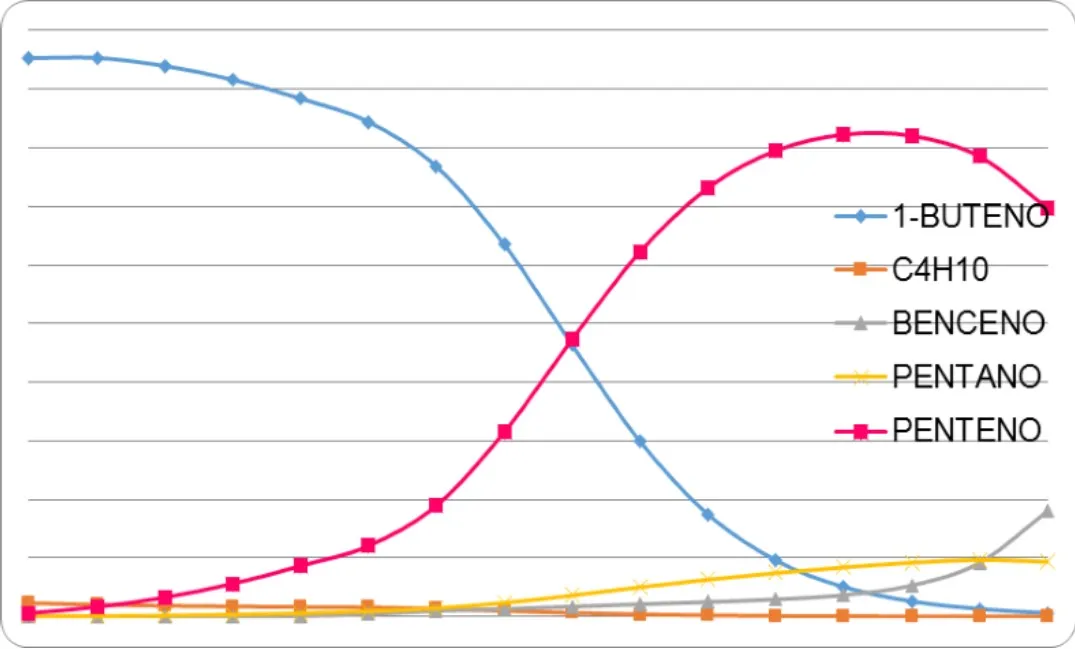
Figura 3. Perfil de la composición vapor típicas en las torres desbutanizadoras.
Fuente: @rossanavictora
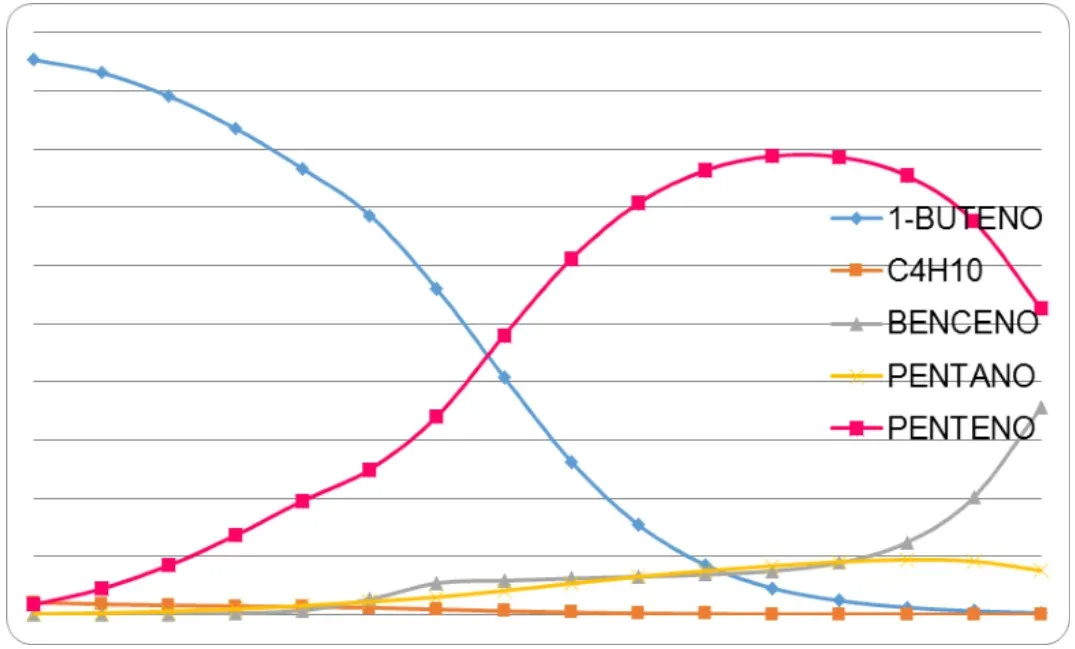
Figura 4. Perfil de la composición líquido típicas en las torres desbutanizadoras.
Fuente: @rossanavictora
Las conclusiones derivadas de esta simulación es la obtención de las composiciones para la alimentación de la torre desbutanizadora por características de diseño típico. De esta forma, se continúa con el estudio necesario para culminar con la investigación de las problemáticas que pueda presentar dicha columna realizando variaciones en su composición y así buscar soluciones que optimicen cada paso del proceso.
Próximamente estaré publicando las conclusiones de esta investigación, con el fin de demostrar las evaluaciones obtenidas de la misma. Para poder prestar diversas observaciones para la mejora de esta torre de fraccionamiento.
Referencias:
- Karen Rosana Romero Harrington (2007). Mejoras del sistema de fraccionamiento propano-propileno de una planta de olefinas. Trabajo de Grado. Facultad de Ingeniería. Programa de Postgrado en Ingeniería de Gas. Universidad del Zulia. Maracaibo, Venezuela.
- https://modeladoysimulacioneniqu.webnode.es/simulacion-en-ee/simulacion-de-procesos-quimicos-usando-aspen-plus/
Si tienes alguna duda o alguna critica no olvides dejar tu comentario.
Gracias