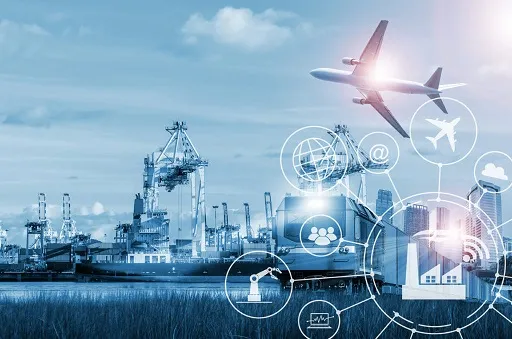
We've seen the prices of certain assets skyrocket during the pandemic and lockdowns. Lumber is just starting to come back down. Many wrongfully attribute these rise in prices to an increase in money supply (inflation). Ironically, even though we are printing out trillions of dollars at the speed of brrrr, the world's reserve currency has lost very little value from this dilution.
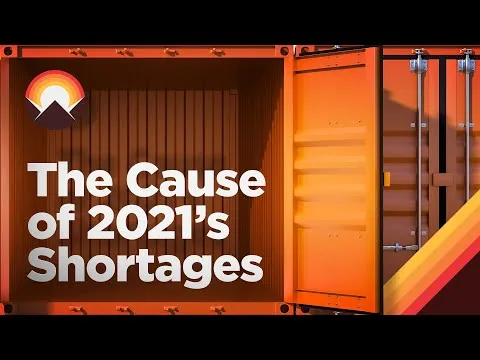
This is the real reason why certain commodities have gone through the roof. It's a 'simple' supply and demand issue. The supplies are low and the demand is high. This video goes into many of the reasons we've seen such low supply for so many products. At the core of it all is the Just In Time logistics model.
Just In Time
This largely self-explanatory model is just what it sounds like. When a factory needs any given asset they need to be provided with that asset "just in time". Companies don't want to have product stockpiled if it doesn't need to be stockpiled, as this stockpiling becomes a huge overhead cost and a waste of potential efficiency.
Apparently this model was invented by Toyota back in the day, and the western world has adopted it and bastardized it. The corporate greed of companies that use this model is the reason prices are so high today. It's been a couple weeks since I watched the video, so I'll rewatch it now and give my summary below.
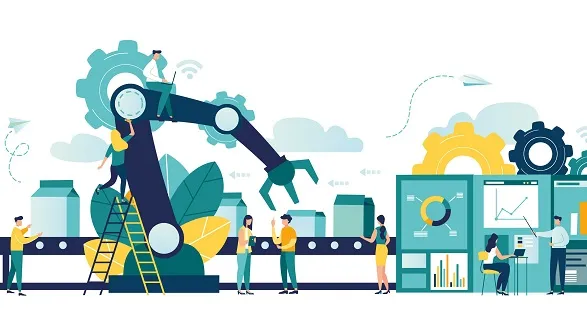
Summary:
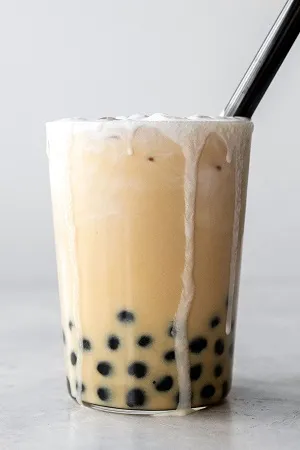
Introduction: Boba shortage.
The Boba Taiwanese tea/coffee drinks that have become so popular in America skyrocketed in price during the COVID pandemic. The interesting thing here is that there was no increased demand for the drink, and the factories that create the Boba pellets didn't even get shut down. The question we must ask ourselves is: how was supply slashed so badly?
Transit time from Taiwan to Los Angeles is typically around two weeks, so an additional 10 days is a near doubling of shipping times.
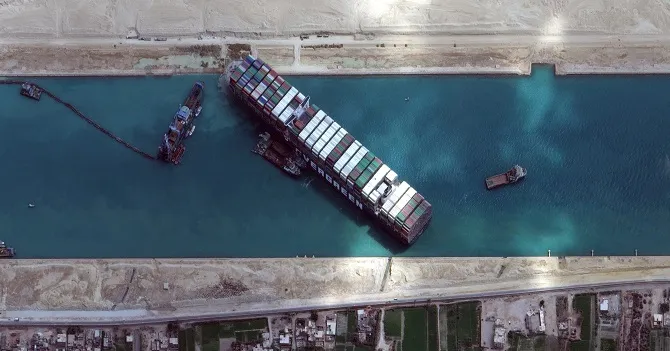
Yeah, remember this bs?
So even though the factories were up and running the time it took for products to actually reach their destination was vastly increased.
But that's not all...
Because so many businesses were shut down during the pandemic, this increased online sales, which in turn increased demand of products shipped over seas. With the two main ports of Los Angeles and Long Beach being totally overburdened (+50% container traffic), again, shipping times increased drastically. It obviously didn't help that dock workers were out sick more often than usual.
But wait, there's more!
The price of shipping containers went from $1800 to $3500.
There's a regional shortage of shipping containers,
resulting in global consequences.
For every 100 shipping containers sent to the US, only 40 are exported.
Containers were constantly piling up in places they weren't needed. Because busy ports like Los Angeles and Long Beach were already extremely overburdened, they didn't have time to send empty shipping containers back to their destinations to be reloaded. On top of this, a shortage of truck drivers made it difficult to even get the empty shipping containers back to the ports in the first place.
Yikes, so many logistics that no one even thinks about.
Boba Tea conclusion:
A shortage of shipping containers,
is worsening a shortage of shipping capacity,
which is worsened by a shortage of port capacity,
which is worsening the shortage of shipping containers,
which itself is worsened by a shortage of truck drivers,
all of which is causing a shortage of Boba tea ingredients.
Yikes.
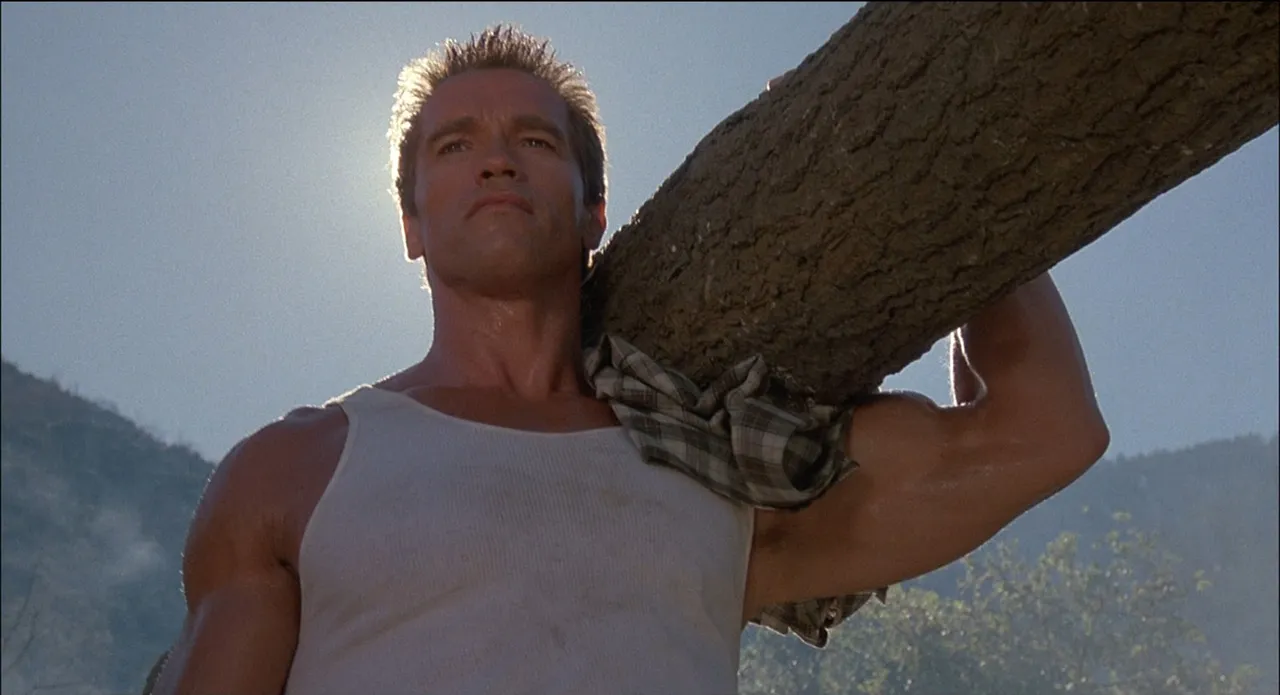
Part 2: Scarcity
Lumber prices quadrupled after a predicted decline failed to manifest, and a boom in construction & renovation did instead.
In addition, the price of chlorine went up due to a rise in demand for pools on top of a factory burning down. Also, catsup packet prices skyrocketed when all restaurants started delivering during lockdown. Factories that made the packets couldn't justify scaling up operations to mean such short-term demand. Capitalism.
Alaska tourism
Alaska, like many parts of the world, relies on tourism to support the local economy. Many cruises were canceled due to legality concerns, and this massive lack of transport skyrocketed the demand for rental cars. Demand for rental cars increased so massively that there were no cars to rent after a very short period of time. Prices increased to $500+ a day just to have access to a vehicle.
During the lockdowns many of the rental car companies needed capital so they sold off a lot of their unused rentals. Now that rentals are in high demand they don't have the cars to supply it. Oops.
It is actually quite common for rental agencies to sell off some cars during the cyclical phases of low demand, and rebuy the cars later when demand increases. However, this time around there are no cars left to buy.
Part 3: Automotive shortage.
Of all the shortages that rocked the world, perhaps the most flagrant one was the computer chips required in every car.
It was the perfect storm of circumstances.
- US trade war with China caused them to stockpile chips.
- COVID led to production shutdowns.
- Lockdowns created high demand for electronics.
- Silicon is needed for both chips and vaccines.
This is why you still can't easily buy a PS5
This is why Samsung likely won't release a new phone this year.
This is why you can't get a rental car in Alaska.
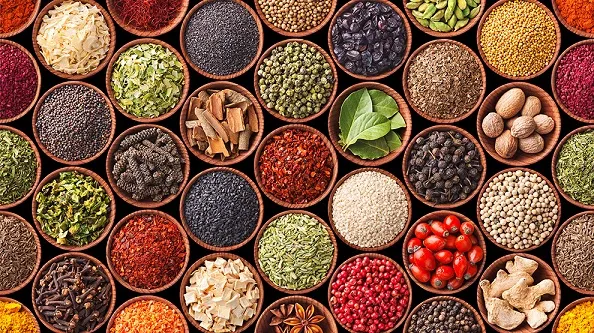
Part 4: Just In Time
This corporate efficiency model is the thing that makes it so easy for supply lines to be disrupted. Apparently after WW2 Japan had to compete with America's scaled up economy. Because demand for things like cars was so much greater in America than smaller countries like Japan it was hard to compete with American assembly lines. Demand for diverse options was much greater in Japan, making mass production more difficult. They didn't have the demand to make batch manufacturing work as well as it did in the USA.
Excess inventory is a waste because it costs money without making money. The Just-in-Time model is a pull system where demand from the front-end pulls product from the backend. This is the opposite of a push system where factories would just run and push their product to the next phase on the line. The pull system creates far more efficiency and far less waste, but is also more prone to supply disruption.
If there are six steps in a manufacturing process, and each holds two months of inventory, it would take a year to pivot to producing a new product.
Obviously, this is not acceptable in todays climate of exponential technological expansion, so the just-in-time pull system becomes an absolute requirement for many industries.
The pursuit of the elimination of waste has become the primary focus of any manufacturing process.
This is what Just In Time is all about, but it has been bastardized by the western world. Rather than eliminating waste, often times companies will eliminate product that they actually should stockpile because not doing so could cause massive supply-chain disruptions, just like it did during the pandemic.
They failed to realize that eliminating excess inventory is different from eliminating all inventory.
They ignored the culture of stopping and fixing problems to get things right the first time.
They ignored the culture of valuing people and reputation.
2011 Earthquake
This quake rocked Japan's infrastructure (including chip production), so when COVID hit in 2020, companies like Toyota were ready. Toyota knows which products can be substituted (plastics) and which ones can't (chips).
Plastic resin can handle disruption, semiconductors can not.
So Toyota is essentially the only car manufacturer that didn't get hit by the chip shortage. Expect to see a lot of Toyotas :D
Conclusion
Disruption is inevitable. The pandemic has taught companies all around the world that constantly taking short-term gains is bound to blow up in their faces eventually. The Just-In-Time logistics model is a good one when implemented correctly, but very few companies have actually achieved such a complex feat. It's a constant battle between efficiency and robust resistance, just like crypto itself.
I hope that we can all see now how blatantly the economy is constantly oversimplified by those who refuse to do the proper research. How many peers have you personally seen attribute the rising price of assets due to printing money out of thin air? Oh, if only it were that simple.
In 2020 I described the pandemic as a slow-moving train wreck that I couldn't look away from. That train is still in the process of being completely derailed. We haven't even come close to recovering, and I hope that this video and my analysis of it shows why. By all accounts 2022 could be the Everything Bubble. Or maybe not, who knows?
There are thousands upon thousands of variables all interacting at once in the most chaotic way all at once. That is the nature of emergent network effect combined with Chaos Theory. It is nearly impossible to predict how/when/why things happen once these systems get complicated enough. All we can do is try to learn as much as possible and make our best guess.