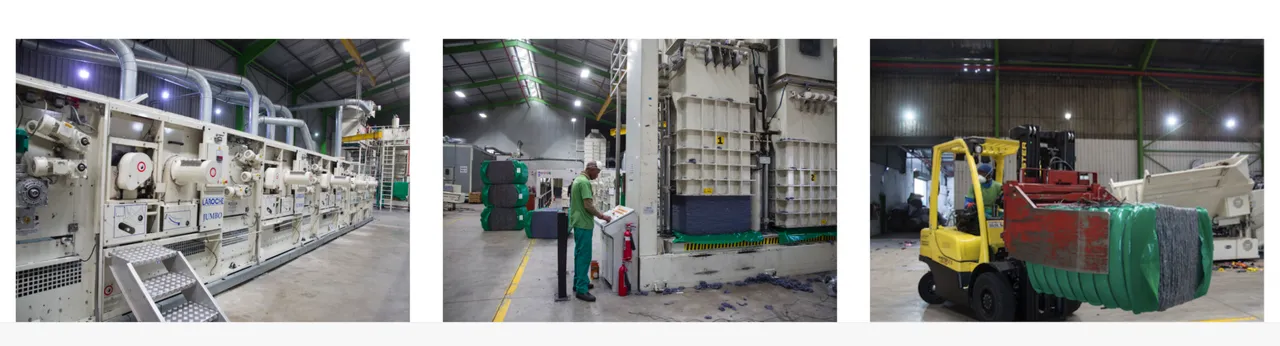
The various steps are receiving the textile waste before using giant magnets to remove any metal. The material is then washed and dried before going to a shredder and then a textile /thread separator. My textile waste finishes at step 4.
No source link for these images as I need to keep my suppler secret and searching via Google Lens does not link back to these images. This supplier search involved a good 6 month search.
My textile waste supplier set me an invoice yesterday which has already been paid for only 10 tons of material. My order was for 32 tons, but they are being over cautious making sure what I have ordered is exactly what we want. They were exactly the same with the sample and the order would not be placed until I had confirmed by sending them a video of us testing their material out.
This is not something I have encountered before as normally companies are looking for the sale and do not care what happens afterwards. Money grabbing comes to mid but these guys are he complete opposite. This may be slower doing business with this company, but you have to hand it to them that they do care you are getting what you want. This is very rare in todays world and they may actually be a pleasure to work with or a nuisance lol. I say nuisance as the last thing I need is to be held up receiving my orders due to how they operate. Then again they are guaranteeing you are totally happy with their product and a customer for life.
If you consider I have already agreed it is exactly what we want and yet they are only supplying 1/3rd of the order and what went through my head was maybe they are stalling. I do not think this is the case, but this is not anything II have encountered before and just have to go with the flow.
This delay first order actually benefits myself as firstly I am only forking out only 30% of the expected payment and secondly I do not requires so much storage space. 10 tons will be 6 cubic meters so the same as a 20 ft container.
Putting things into perspective 32 tons would most likely supply roughly 8 weeks of production ad if I can receive 10 tons regularly it would make thigs far simpler. When I was sourcing the textile waste earlier this year we had never actually stuffed a punch bag before and the use of river sand was only a thought. Now we know we actually do not require the 32 tons in one hit but if that is the only way the I will gladly accept it.
Over the last 3 weeks I have used slightly over 17 tons of stuffing which has been a 50/50 mix of textile waste and river sand. The big difference is the quality of this material making it user friendly which will peed up the entire stuffing process ultimately reducing the costs increasing the profitability.
Our clients who we are supplying will see the difference ad any new client which we have some stopping by soon for an audit will be immediately sold on what we are doing. Our competitors do not have what we have and this has to be seen as a game changer making us stand out for all the good reasons.